Superbike-WM – digitale Technik ist immer wichtiger
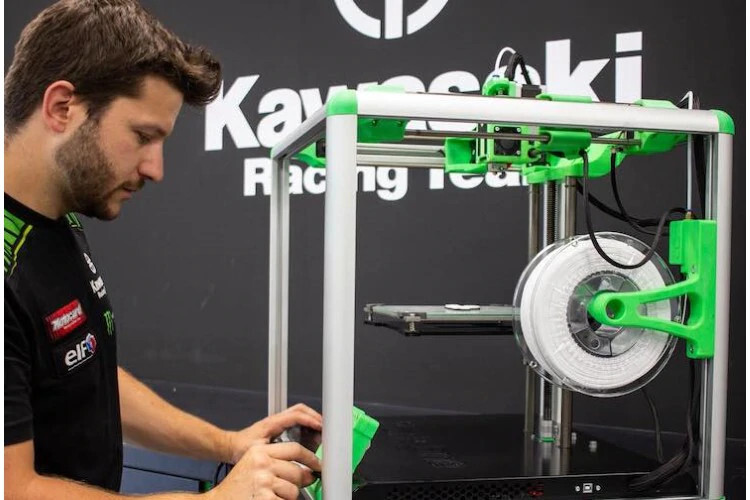
Ein 3D-Drucker wird zum Standardwerkzeug
Das Arbeiten mit Maulschlüssel, Zangen und Schraubendreher an Motorrädern wird es immer geben, doch um die letzte Zehntelsekunde herauszuholen, werden digitale Techniken immer wichtiger. Sei es in Form der Elektronik und der Daten-Analyse, aber auch bei der Konstruktion und Weiterentwicklung.
So gehört ein 3D-Drucker bei den besseren Teams mittlerweile zur Standardaustattung in der Box. Das Kawasaki-Werksteam hat sich dafür mit der Firma Mark One als technischen Partner verbündet; auch BMW arbeitet mit der 3D-Druck-Technik. So können in Windeseile Ersatzteile oder Weiterentwicklungen gedruckt werden und kurz darauf auf der Strecke verwendet werden.
«Mit dieser Technologie können wir schnell und effizient Verbesserungen an der RR vornehmen. Die Weiterentwicklung eines WM-Bikes ist ein fortlaufender Prozess, und häufig sind es kleine Details, die ein Motorrad besser machen», sagt BMW Motorrad Motorsport Direktor Marc Bongers. «Mit Hilfe des 3D-Drucks können wir das an der Rennstrecke auch während Rennveranstaltungen direkt und schnell umsetzen.»
Und um die Aerodynamik zu verbessern, benötigt man nicht zwingend einen Windkanal mit Turbinen als Windstromerzeuger. Hier nutzt Kawasaki seit 2017 die Expertise der Firma Puig. Das spanische Unternehmen produziert Zubehör (Verkleidungsscheiben, Spoiler, Hinterradabdeckungen usw) für verschiedene Motorräder und entwickelt seine Teile in einem virtuellen Windkanal.
Die Zusammenarbeit mit Puig wurde jüngst verlängert. «Das war obligatorisch», betonte Biel Roda vom Kawasaki-Werksteam. «Sie sind die perfekten Technik-Partner und bringen uns eine sehr positive Entwicklung mit ihrer 3D-Simulationstechnologie sowie der Rennleidenschaft und ihrem Wissen. Der Firmensitz befindet sich in unmittelbarer Nähe zu Provec Racing. Operativ und menschlich sind wir uns also mehr als nah.»
BMW nutzt den firmeneigenen Windkanal in München, die Fahrer müssen dafür aber nicht mehr auf der M1000RR Platz nehmen; dies erledigen lebensgroße Modelle aus Plastik, die mittels 3D-Lasermessung erstellt wurden.
«Auf Basis der Daten aus dem 3D-Scanning haben wir ein aus zwei Hälften bestehendes Kunststoffmodell erstellt. Bis dieses detailgetreu fertig ist, dauert es etwa eine Woche», sagte Bongers.